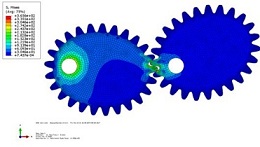
发动机将内啮合齿轮应用于膨胀机。但目前对内啮合转子膨胀机的结构设计和工作特性研究上比较薄弱,从膨胀机的失效情况来看,内啮合齿轮是最容易出故障的零件之一,因而有必要对齿轮工作接触状态下的强度性能进行合理的评估。利用有限元分析软件ANSYS,对内啮合齿轮建立比较精确的分析模型,准确掌握齿轮接触应力分布特点,得到的研究结果对内啮合转子膨胀机中齿轮的设计和提高设计效率具有重要意义。
内啮合转子膨胀机齿轮设计参考齿轮式油泵相关型线的设计过程与方法,采用完整的连续封闭的短幅外摆线的等距曲线作为内转子齿廓,外转子采用与其共扼的均布圆弧作为齿形。经实验讨论拟用基本参数如表。经计算得到其几何尺寸参数如表,利用Pro/E软件建立齿轮的几何模型,将建好的2个齿轮进行装配。装配好的齿轮模型如图,所示因为该膨胀机的最高温度可达到600℃以上,所以选择耐高温的材料。本文选择是高温合金GH4169,弹性模量206GPa,泊松比为0.30,将齿轮在Pro/E模型转化为ICES格式导入到ANSYS中,将齿轮划分为三个部分:接触区域、接触相邻区域、非接触区域,对接触区域和接触相邻区域适当的加密。选择smartsize智能网格划分,6级精度,单击mesh,选择所要划分的两个齿轮。然后在齿轮啮合处进行局部加密,得出最终划分出来的自由网格模型为如图。用TARGE169和CONTA171或CONTAN172定义2D接触对。用TARGE170和CONTAN173或CONTAN174定义3D接触对。
将内齿轮外廓边界上的节点X,Y,Z方向的位移设置为零,即约束内齿轮的径向自由度、外齿轮的径向和转向自由度。由于采用接触模型计算,载荷可以直接施加到内齿轮。将啮合内齿轮的齿廓线2和外齿轮的齿廓线1设置为接触对:齿廓线1为接触面,齿廓线2为目标面。将其接触刚度因子FKN和拉格朗日算法允许的最大渗透量FTLON分别设置为1.0和0.1。接触对设置见图。在内啮合齿轮膨胀机中,主动轮内转子通过轴输入转矩传递给外转子。对外转子和内转子的内圆面施加位移约束,约束X轴,再约束外齿轮安装孔表面上所有节点的自由度;同时在内转子内圆面施加转矩,输入五的值为243N(以发动机功率100kW计算得出)。在实际工作状况中,需要考虑转子膨胀机在齿轮啮合情况下,7个工作腔内的气体对内外转子产生接触应力的影响。由于若考虑气体压力,对计算机的硬件要求过高,且求解繁琐,耗时过长,所以不予考虑。
在内外齿轮啮合的情况下,对内转子施加243N的扭矩,使其绕中心轴进行顺时针转动。由静应力分析图可得知:最大应力在接触面1上,该处的齿轮最大应力主要集中在外齿轮齿顶处与内齿轮齿根处,达到了946.582MPa,并逐渐向周围扩散减小。接触面2上齿轮的应力相比于接触面1已经大幅减小,最大应力值降低为631.002MPa。接触面3处内齿轮齿根处受力为210.352MPa左右,已大幅度下降。接触面4内外齿轮啮合处应力都发生在齿顶处,集中在一个极小范围内为105.176MPa。接触面5、接触面6、接触面7处几乎不受力。
通过应力云图可以看出齿轮在接触点和齿根处应力集中,最容易发生破坏。由图比较可知,在内啮合转子膨胀机工作情况下,接触面1受到的压力最大,也最容易发生断裂,尤其在内转子的齿根圆角处。这是因为主动轮为内转子,内转子带动外转子时,接触面1处于完全啮合情况下,传动效率最大,所以在此处产生的接触应力最大。同时接触面1也处于工作腔满载荷情况下,此时压力达到最大,理论值约为6atm,接触面1不仅受到内外转子完全啮合产生的接触应力,同时还受到了高压气体对齿轮产生的压力,此处最容易折断,这是膨胀机工作情况下最容易发生故障的原因之一,其余6个接触面的接触力逐渐减小18]0本实验采用了高温合金GH4169,该材料在高温时有较大屈服强度,符合实验要求。为了减小内转子的齿根处的应力,可以对齿轮结构设计时改变其参数,加工时进行热处理和加大局部工艺强度等。
1)在高速工作情况下的膨胀机每个接触面都在不断交替承受着较大的作用力,所以在材料选择方面,需要选用高强度的材料,本文采用高温合金GH4169符合实验要求,传统的45号钢很难达到强度要求。2)内啮合齿轮式膨胀机内转子的最大应力发生在齿根的圆角处。在齿轮啮合过程中,此处最容易折断,这是膨胀机工作情况下易发生故障的原因之一。3)根据以上的数据分析,对内啮合齿轮膨胀机的齿轮结构的设计、参数的优化和强度的校核方面提供一定的参考价值。
专业从事机械产品设计│有限元分析│强度分析│结构优化│技术服务与解决方案
杭州那泰科技有限公司
本文出自杭州那泰科技有限公司www.nataid.com,转载请注明出处和相关链接!