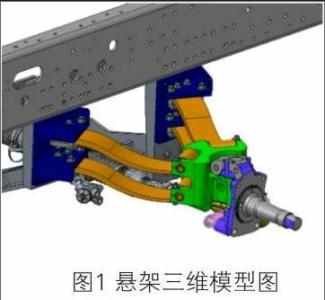
在汽车产品的研制过程中,需要对零部件进行大量的强度与耐久性试验,包括台架试验和整车道路试验,这些试验不仅试验费用高、周期长,而且问题大多是出现在产品具备样件之后,对设计更改带来一定的难度。通过有限元分析,可以在产品设计初期或产品实现前对结构强度进行粗略评价,找到结构的薄弱环节,提出合理的改进方案。
强度分析的内容是反映结构抵抗破坏能力的一种标志,进行悬架强度分析是因为所有来自路面的载荷都要由悬架作用至车架或车身。悬架是汽车重要的承载部件,其结构强度是设计过程中需关注的重要内容之一,悬架必须要满足一定的强度要求。
悬架强度分析常用的2种方法为:零部件级分析方法和系统级分析方法。采用多体动力学方法得到悬架硬点载荷,对单一结构进行分析的方法称为零部件级分析。零部件级分析方法原理简单,而且容易将分析过程流程化、规范化,从而保证分析结果的准确性和一致性。一般来说,在整车开发的初期,最初确定的是一些重要硬点(部件与部件之间的连接点)的位置及相关参数,然后由设计人员根据这些信息对相关零部件进行初步概念设计,在此阶段需要对单个零部件的结构强度及耐久性进行分析,并针对存在的问题提出改进意见,指导结构设计,使之逐步趋于合理。从分析规模上来看,单个零部件分析的计算时间短,占用空间小,对计算机的性能要求不高,比较适合于设计初期结构改进中的多次反复分析验证。首先,对于大多数底盘零部件的分析来说,需要相关的受力分析提供载荷输入,可以通过多体动力学分析计算输出得到相关硬点的载荷。其次,在单个零部件的分析中,边界条件是一个很难处理的问题。边界条件的正确与否,直接影响到分析结果的可信度。因此,零部件级方法要求分析人员对分析对象的各种特征、连接关系以及作用等有深刻的认识。最后,当结构应力超过材料的屈服极限时,该方法不能给出正确的分析结果。这是因为多体动力学不能考虑结构本身的塑性变形,多体动力学即使引入柔性体,也仅限于线弹性变形范围,因此,当结构出现塑性变形时,应用多体动力学方法无法得到正确的载荷数据,更无法保证应力结果的正确性。获取整车相关参数*建立前/后悬架或整体的多体模型*动力学分析提取硬点载荷*代入有限元模型中分析求解。
以整个悬架为基础,同时考虑衬套、限位块刚店以及零部件间相互运动的影响的分析方法称为系统分析方法。系统级分析方法由于能够考虑几乎所有悬架本身特性,如非线性连接关系、运动关系等特性,因而可以得到更为准确的分析结果。单个零部件的先析只能考察零部件的品质,很多零部件连接在一起,成一个系统后,还要对整个系统的结构可靠性进行先析,即系统总成分析。一般来说,系统总成的分析是在系统各个零部件的几何模型确定后进行的。在系统总成的分析中,各个零部件都是以柔性体的形式存在,可以考虑各个零部件的变形对其他相邻部件的影响,同时部件与部件连接处的模拟更接近真实情况,因此与单个零部件分析相比,总成分析的结果精度更高,指导意义更大。另外,从边界和载荷条件来看,系统总成的约束条件比较简单,工况载荷比较容易计算。在悬架总成分析中,只需要对悬架与车身的连接点进行约束就可以了,载荷主要作用在车轮中心,根据整车的相关参数可以很容易求得。
专业从事机械产品设计│有限元分析│强度分析│结构优化│技术服务与解决方案
杭州那泰科技有限公司
本文出自杭州那泰科技有限公司www.nataid.com,转载请注明出处和相关链接!