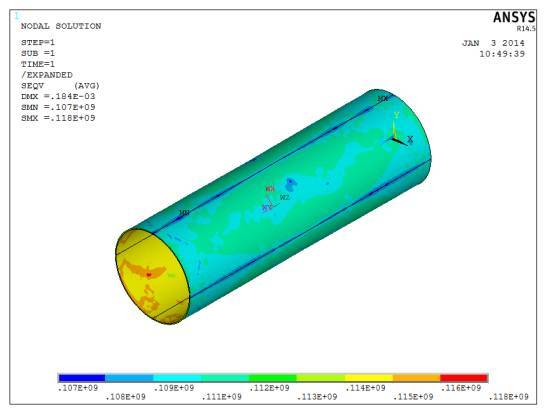
液压胀形技术是一种以液体作为传力媒介,利用液压力或两端轴向力共同作用下使管坯成型出所需加工零件的塑性加工工艺。在德国、美国等发达国家,此项技术已有一些研究,并且已经应用在航空、汽车、化工、机械等各行各业的领域。
随着时代的发展,人们对于安全性的重视程序越来越高。吸能元件在人体防护和结构安全方面起着关键的作用。车辆行驶安全、重装备空投、航天器软着陆、直升机起落、核电站防护和电子产品或贵重物品的包装等领域对材料和结构的能量吸收皆提出迫切的需求。变径管主要采用铸造和焊接的方法来生产,但这些方法原材料利用太低,生产成本高。因此本文针对现有的成形技术,提出采用液压胀形的方法,并且提出折叠的工艺,实现胀形与折叠在一副模具中实现。但是这一变形系统是一个非稳定的成形过程。要使管材在胀形与折叠当中不发生屈曲、褶皱和破裂等失效形式的话,精确控制液压胀形与折叠成形过程中的加载路径是十分重要的。文中用有限元分析软件对液压胀形与折叠进行有限元模拟,以变径管吸能元件成形件的最大减薄率和均匀度作为评价标准,分析加载路径对成形质量的影响,通过模拟得出最优的加载路径。
将管坯放入成形模具中,通过左右两端冲头将管材放入下模中,然后通过两端的冲头将其密封,随后上模向下模移动,与下模接触,形成一个封闭模腔。随后液压油从两端冲头进入到管材内部。两端冲头通过设定,给两端进给,使管坯在型腔内完成液压胀形。完成胀形后,内压保持不变冲头继续进给,完成折叠。
一般的变径管是通过液压胀形成形出零件,本文采用变径管吸能元件的成形在一副模具中一次完成,成形阶段分为两部,首先是液压胀形,完成后继续通入液压油完成液压折叠阶段,并且在液压胀形过程中首先要保证管材的长度;而后液压折叠要保证壁厚和折叠圆角半径,就是要满足吸能元件在成形后的折叠圆角半径与在进行自由翻转产生的翻卷圆角半径的一致性。因此,在设计开发变径管吸能元件时,一次成形两幅吸能元件,这样成形出的零件壁厚均匀,又可以节省不必要的成本和时间。
管材液压胀形的主要工艺参数包括初始屈服压力、开裂压力、整形折叠压力、轴向进给力、合模力和补料量。图2所示的是所要成形后的变径管零件图。成形区直径D为56mm,成形区长度为100mm,零件长度为200mm,最小圆角半径为2.5mm,管材外径为40mm,壁厚为1.4mm。
首先本文对成形零件进行分析,依据零件的特点,因为变径管符合轴对称的要求,因此建有限元模型对于Y轴中心对称模型,又为以后方便进行自由碰撞,减少需要切开变径管的仿真工序,将模型又对于Z轴对称。经过与三维实体建模零件模拟结果相比较,在忽略材料各向异性的情况下,三维实体与简化后建模模型结果基本一致。
模型的几何尺寸如下:管坯长260mm、外径20mm、厚1.4mm;模具总长2800mm、模具大径56mm、变形区长100mm,圆角半径3mm;冲头直径为20mm。网格划分:厚度方向取网格数为3,长度方向取网格数为300。
按照材料的本构关系,管坯可选择理想刚塑性,在管材液压成形模拟中,采用满足Misse各向同性屈服准则和Hill厚向异性屈服准则的弹性材料模型。模具和两端冲头的材料模型为解析刚体。
专业从事机械产品设计│有限元分析│CAE分析│结构优化│技术服务与解决方案
杭州那泰科技有限公司
本文出自杭州那泰科技有限公司www.nataid.com,转载请注明出处和相关链接!