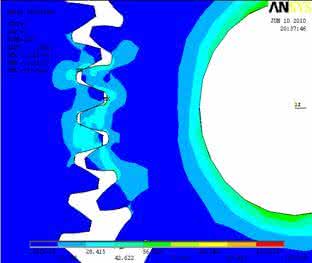
转盘是钻机最重要的设备之一,针对石油钻井工艺的发展,超深井、水平井和定向井对转盘性能的要求日渐严格。转盘的性能直接决定着钻机钻进能力,转盘的研究生产直接关乎我国是否有能力自主研制万米以上的钻机设备。而锥齿轮作为转盘中的主要部件之一,它直接决定了转盘性能的好坏。锥齿轮失效的主要原因之一受载轮齿齿根圆角处的弯曲应力过大造成的,这些应力往往使齿轮的总寿命缩短,甚至使齿轮突然发生断裂。
通过Pro/E软件建立转盘锥齿轮三维实体模型,采用ANSYS软件建立相应的有限元模型,实行加载求解,进行齿轮应力有限元分析,并与传统计算方法比较,这种方法为圆锥齿轮的精确设计提供了可靠的依据和方法。以转盘中小锥齿轮为例,首先在Pro/E中创建精确模型,为了便于在有限元分析中划分网格,应当忽略掉那些在三维实体中不重要的小线,小面,因此,在Pro/E界面下,建立锥齿轮的三维实体模型的过程中,忽略了齿顶和齿根处的倒角。
由于只需分析一个齿廓的受力情况,同时减少划分单元和运算时间,所以采用1/4齿轮建立有限元模型。选用SOLID187单元类型,弹性模量E=2.06 GPa,泊松比P = 0.3,材料密度7900 kg /m。采用24 mm固定尺寸自由网格划分整体网格,并对所分析齿的齿面进行网格细化,划分结果得:7526个单元,12117个节点。
研究详细地介绍了钻机转盘锥齿轮的实体建模及齿轮应力静态分析有限元方法。将Pro/E与ANSYS两种软件相结合,充分发挥了各自的优势,并且,将结论与常规计算应力方法比较,相互验证。完成计算后,通过ANSYS通用后处理器观察齿根弯曲应力等值图。表示载荷步终止时间1,子步数1,时间1的等效应力图,图中显示最大位移为0.469e-2mm,最小应力为0.01063MPa,在齿根位置处的弯曲应力最大,为150.758MPa,这与常规计算150.86MPa基本吻合,这说明在分析转盘大直径锥齿轮中所使用的传统计算方法是可用的,只是结果略显偏大于有限元法。
专业从事机械产品设计│有限元分析│强度分析│结构优化│技术服务与解决方案
杭州纳泰科技咨询有限公司
本文出自杭州纳泰科技咨询有限公司www.nataid.com,转载请注明出处和相关链接!