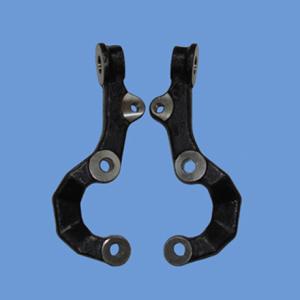
转向节臂是汽车转向系统中的重要安全件,在车辆运行中起着承载、导向的功能,其失效将导致汽车无法转向而引发严重的事故。因此,为了保证汽车在高性能的要求下有足够的强度,对转向节臂的进行有限元分析是十分必要的。查目前国内关于转向节臂强度的研究文献,大体可以概括为三个方面:①改进转向节臂的成形工艺及热处理方法,改善其组织性能,借以提高转向节臂的强度;②运用仿真软件对转向节臂的强度、刚度及疲劳性能进行模拟分析;③通过理论计算的方法对转向节臂的强度进行分析。重载汽车的转向节臂的结构复杂,承受荷载复杂,理论计算结果过于粗糙,目前的数值模拟分析文献对载荷部分的处理还过于简单,一般都是在接触弧面施加均布荷载,模拟结果误差较大。研究主要利用ANSYS分析软件,采用参数化命令处理非线性的载荷约束,对重载汽车转向节臂进行静力强度分析,并对结构进行优化设计。
汽车转向系工作时承受的载荷主要来自人为施加在转向盘上的力和来自地面的转向阻力两方面。对于重载汽车转向节臂,转向盘上作用力较大。施加在转向盘上的力,通过转向轴、转向器、转向垂臂和转向直拉杆传递到转向节臂的球头弧面上。关于转向节臂在工作时承受载荷的计算,涉及到的一些设计参数,如表所列。根据设计参数及传动关系,依据计算出转向器从动齿轮轴所承受的扭矩T,转向垂臂端部承受的力F,转向节臂右端孔处受得力F。根据关系式F=T/L,计算出F为7200N。孔与轴之间是面与面的接触,受力形式主要是分布力,根据受力面大小,得到载荷的大小,分布载荷形式不同,得到的载荷大小也不相等。以某种工况为例,根据公式A=,rRh,式中R为圆孔的半径为0.01m,h为圆孔的深度为是0.023m,计算得到面积为0.0007222m²。
转问节臂与转问节相连接的部位是圆锥白,通过端部螺纹定位,在建立重载汽车转向节臂的有限元模型时,考虑到端部螺纹定位部分受载较轻,完全按照实际的结构尺寸建立螺纹模型,需要花费大量的时间确定其曲面曲率以及倒角的尺寸,给网格化及其分析计算带来较大麻烦,在建模时忽略螺纹部分。同时零件上便于装配的一些倒角对分析产生的影响很小因此也可忽略。根据研究形状的几何特点以及有限元分析时约束条件,合理地简化结构形状复杂的零件模型。采用常用的三维造型软件Pro/E,通过构建基准面、基准轴,利用拉伸、混合和混合扫描等构建出转向节臂的几何模型,通过Pro/E与ANSYS的无缝集成,将几何模型导入到ANSYS中,设置材料属性,定义弹性模量以及泊松比,采用Solid45单元,设置网格的边界尺寸,确定了智能划分的粗细精度为6级,采用自由划分对模型进行网格划分。得到转向节臂的有限元模型如图所示。
转向节臂与拉杆之间的接触面是圆弧面,根据材料力学相关资料可知,其上的力是随位置变化的。根据弹塑性力学以及数值分析中的最小二乘法,对转向节臂所承受的载荷约束采用非线性变化的余弦三角函数。根据集中力F和受力面积A,得到载荷变化曲线,施加在与拉杆相连接的半圆弧面上。而与转向节相连接的一端,采用全约束的形式。通过模拟计算,得到了转向节臂的等效应力分布情况,如图所示,转向节臂的等效应力的最大应力点位于转向节臂中间过渡部分;最大应力是230.739MPa。转向节臂中间过渡部分的应力变化最明显,高应力区较大;离过渡区域越远,高应力区就越小,低应力区较大。过渡部分存在最大等效应力,远离过渡部分,等效应力随之减小,实际工作中转向节臂的断裂主要发生在该部位,说明其断裂的主要原因是该部位强度不足引起的。转向节臂的中间过渡圆弧位置受力较大,结构设计是为了提高其强度,可增大过渡圆弧的半径;与转向拉杆相连接的部分,应力变化较小,且多数处于低应力区域。为了节省材料,节约生产成本,提高经济效益,需要对复杂结构转向节臂的结构进行优化处理。对于应力值较小的区域可减小截面积,因此对原有模型进行适当优化处理,运用已有的载荷约束对其优化后的模型进行强度模拟分析,结果如图所示。可看到,优化后的最大应力值减小,最大应力值是204.456MPa,小于优化前的230.739MPa。
专业从事机械产品设计│有限元分析│强度分析│结构优化│技术服务与解决方案
杭州那泰科技有限公司
本文出自杭州那泰科技有限公司www.nataid.com,转载请注明出处和相关链接!