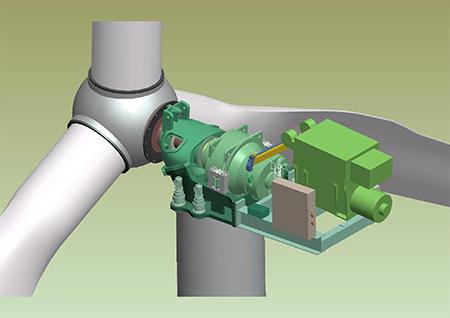
主轴作为风力发电机组传动链系统中重要的组成零部件之一,虽然其结构较简单,但其不仅承载了支承轮毂处传递过来的各种负载的作用,而且要将转矩传递给齿轮箱及轴向推力,气动弯矩传递给机架,其设计的合理性和安全性直接影响到整个传动系统乃至整个机组的性能。由于主轴的受力较为复杂,且零件尺寸大,因此一般采用有限元分析法对主轴进行强度分析,此方法在主轴设计过程中可以缩短研发周期,同时节省研发成本。主轴的失效模型主要有两种:①由于承受极限载荷过大,在主轴局部区域材料产生塑性变形而破坏;②因主轴所承受的交变载荷过大,在设计寿命20年出现损伤超过设计值,产生疲劳破坏。文献中虽对主轴进行静强度分析,但其分析边界中未建立主轴轴承内、外圈及考虑轴承滚子对主轴强度的影响,我们通过建立主轴强度分析模型,首先对主轴进行在极限载荷工况下的静强度分析,之后进行在主轴设计寿命内的疲劳损伤计算,为主轴设计提供一种具有指导意义的依据。
主轴在风力机中的布置方式有多种,本研究中其布置型式如图所示。双列球面轴承的内、外圈分别与主轴、主轴承座过盈装配。使用三维建模软件SolidWorks建立主轴、风轮锁紧盘、轮毂假体及涨紧套几何模型,并进行装配,主轴几何模型如图所示。首先根据分析要求对主轴进行几何清理,简化主轴与轮毂连接螺栓孔及主轴与锁紧螺母配合的螺纹,之后对主轴、轮毂假体、风力锁紧盘及涨紧套进行网格划分,图为主轴有限元分析的网格模型,图为主轴的局部网格模型。网格总体数量为959651,其中四面体网格172887,五面体网格64164,六面体网格7226000,主轴强度分析时的载荷边界值是使用Bladed软件根据将作用在风轮叶片上的力及力矩通过坐标转换至轮毂旋转坐标系下所得到的,其中风力叶片上的力和力矩需根据叶素理论来求解。
为了模拟主轴承受的力及力矩,在轮毂中心建立节点,通过刚性连接至轮毂。主轴承系统(主轴承、轴套、锁紧螺母、轴承座等)将轮毂中心的轴向推力传递至机舱,因此对轴承模拟时使用只受压不受拉的单元,模拟方式如图所示。图为主轴强度校核时所使用的旋转轮毂坐标系。表为施加在轮毂中心节点处的极限位移边界条件。因主轴外圈与轴承座过盈装配,因此将主轴承外圈固定约束,同时约束扭力臂中心处除轴向方向的平移自由度及主轴绕X轴旋转自由度。通过使用有限元求解器对模型进行求解,得到在极限工况Nftrcmax下主轴的VonMises应力分布情况。主轴材料屈服强度为490MPa,根据GL规范中对主轴的设计要求,考虑材料1.1的安全系数,主轴材料所允许的应力值为445MPa,根据分析结果可知,主轴的最大VonMises应力值为399.2MPa<445MPa,因此主轴的静强度满足设计要求。
在GL规范中规定风机中承受交变载荷的零部件均要满足20年的使用寿命(循环次数一般为1X10次),因此在主轴设计中根据主轴所承受的交变载荷及主轴材料S-N曲线,并依据线性损伤累积法则对主车由进行疲劳寿命计算。本研究文中载荷谱的获得是Bladed软件计算的结果,载荷工况共153个,图是主轴某一疲劳工况的载荷时间历程图,在计算主轴疲劳寿命时,所使用的有限元模型同极限强度的分析模型,只是在轮毂中心点施加单位载荷数据。表为在单位载荷下主轴上各个热点的应力值及热点位置,此热点处的疲劳损伤一般较大。主轴的材料为34CrNiMo6,其材料的S-N曲线拟合过程参照参考文献,在S-N曲线拟合过程中所考虑的折减影响因素主要有应力集中系数、缺口影响系数、部件尺寸、表面影响、工艺参数影响、存活率及环境条件等。锻件S-N为文献规定的无焊接锻件及曲线,根据文献中的拟合过程所拟合的S-N曲线如表所示。根据分析流程,对主轴进行疲劳寿命分析。
专业从事机械产品设计│有限元分析│强度分析│结构优化│技术服务与解决方案
杭州那泰科技有限公司
本文出自杭州那泰科技有限公司www.nataid.com,转载请注明出处和相关链接!